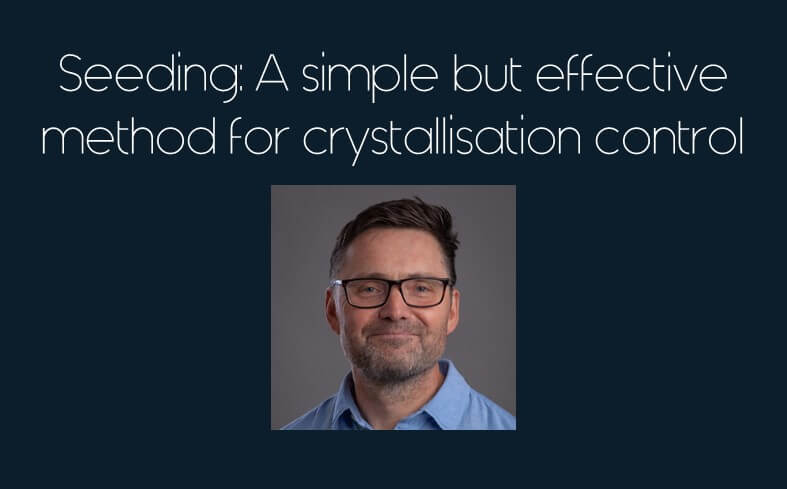
Seeding: A simple but effective method for crystallisation control
Seeding is probably the most common technique for controlling the solid-state and physical properties attributes of a drug molecule. But what needs to be considered when using seed crystals?
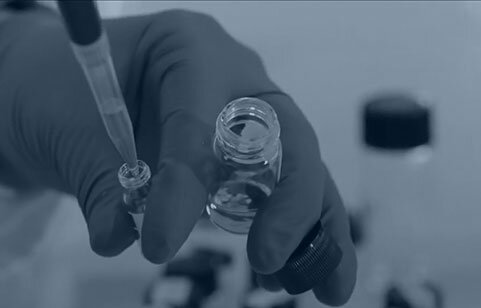
Identify what needs to be controlled
There are 2 main reasons for using seeding in pharmaceutical crystallisation:
Control of solid-state form is the most common reason. The assumption being that the form of the product is templated by the addition of the seeds. Without seeding, nucleation may generate an undesired solid-state form which alters solubility and formulation performance.
Control of particle size is less common in my experience but is a much more elegant solution to control of Particle Size Distribution (PSD) than the alternatives, milling or micronisation. Dry milling methods add process complexity, are dusty and hence require containment.
In addition, seeding may be utilised to better control supersaturation where this is linked to a specific undesirable effect such as impurity incorporation, agglomeration, or oiling.
The seed source
A variety of seed sources can be used:
- ‘As-is’ seeds from a specific batch – a batch is identified and used to seed many batches.
- Daughter seeding – seeds from the preceding batch are used for a specific crystallisation and this is repeated with subsequent batches.
- Milling or micronisation – a batch is size reduced and used to seed many batches.
- Sieve fractions – a batch is sieved to deliver a fraction and used to seed many batches.
Selecting the seed source depends on the attributes in the product that require control. For solid-state form, any seed source can be used. For control of PSD, the seed itself should be size controlled and hence only milling, micronisation or sieve fractions are viable options. Whichever source is selected, the seed batch should be well characterised using a battery of analytical techniques to ensure phase purity and appropriate PSD.
The use of daughter seeding carries the risk of progressive build up in the seed of an undesired solid-state form and this option should be used very cautiously.
Process development
Ideally, the solid-state form landscape of the molecule should be well understood before seeding is instituted. As well as this, the process, preferable a cooling crystallisation, should be well designed with selection of the appropriate solvent and determination of the solubility curve and metastable zone width. With this data, an appropriate point on the solubility curve can be determined for seed introduction. A simple rule of thumb is to seed 1/3rd into the metastable zone. The trajectory of the crystallisation should then be controlled to limit the build-up of supersaturation and hence avoid nucleation and limit agglomeration. The objective is always to maximise growth of the seed crystals.
Where PSD control is an objective, the effect of adding increasing amounts of seed should be studied. The crystallization can be biased towards crystal growth if a correlation is found between output PSD and seed loading. If no correlation is achieved, then nucleation may dominate the crystallization and an alternate strategy will need to be investigated. Once the seed loading has been established the impact of agitation should be assessed. This plays a role particularly for agglomeration and attrition and both should be limited. The process can then be cautiously scaled using the standard consideration of geometric similarity and using appropriate scaling parameters with the output PSD being measured at each step.
Introducing seeds into the crystallisation
Seed crystals need to be introduced into as homogeneous environment as possible and carefully grown, avoiding excessive build-up of supersaturation in the bulk. This is addressed partially by appropriate cooling and suspension conditions, but how the seeds are introduced is also important. The seed crystals should be well dispersed at the point of addition and slurrying the seeds in a solvent is an ideal method to do this. Slurrying may alter the seed physical properties so this step should also be studied, for example, using laser diffraction and SEM. The seed slurry should be introduced into a portion of the vessel which is the well mixed and CFD modelling may be useful in assessing the best point of addition.
Stability of the seed source
A shelf life for the seed should be nominated and supported by physical properties data indicating that the seed is stable and functional over time. Use testing of the seeds in the crystallisation may also provide useful data to support shelf life
CatSci project teams work collaboratively to integrate process chemistry solutions with key decisions in formulation development.
Want To Find Out More?
Watch our symposium: Material Science in Drug Development: A Holistic Approach
Contact us at enquiries@catsci.com or explore our capabilities.
You can find Robert’s blog post on how to make sure salt screens are as effective as possible here.
Author: Robert Dennehy, Director of Material Sciences at CatSci Ltd.