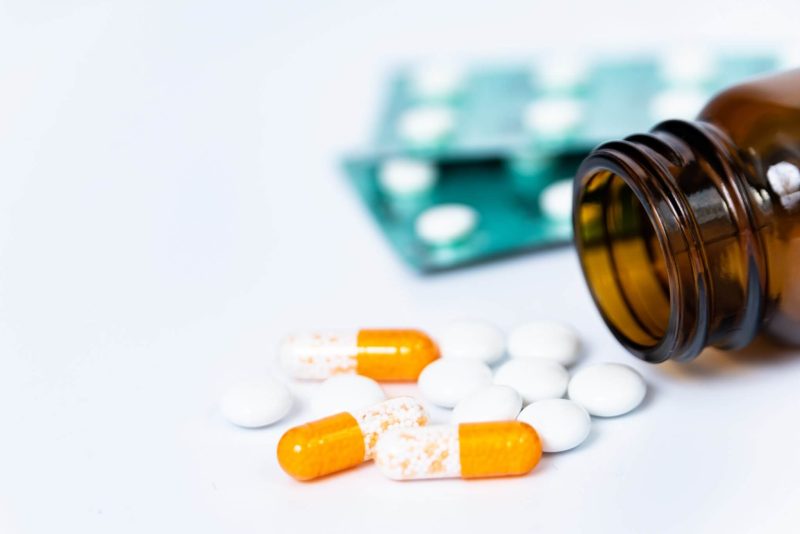
Introduction to Nitrosamine Contamination
2019 saw a wave of recalls of blood-pressure regulating drugs containing a class of compounds known as “sartans”. Both the FDA and the EMA raised concerns in July 2019 about Valsartan, an API manufactured by Zhjiang Huchai Pharma, because of the level of N-Nitrosodimethylamine (NDMA) it contained. NDMA is classified as a probable carcinogen even at extremely low concentration and therefore its presence in an API, such as Valsartan, justifiably raised a red flag. This recall led to drug shortages in several countries, leaving doctors and patients scrambling for alternatives.
NDMA in Valsartan was not the only case of nitrosamine contamination in sartans. N-Nitroso-N-methyl-4-aminobutyric acid (NMBA) was also detected in Losartan in 2019. Nitrosamines obviously represent an elevated risk to patients and therefore every effort must be made to ensure the safety of the API supply chain.
The Valsartan Case
In the case of Valsartan, issues arose after an undisclosed change to the manufacturing process. However, the source of the issue is believed to lie in the tetrazole ring formation step. That transformation typically involves reacting an azide with a nitrile, under ZnCl2 catalysis with DMF as solvent. Sodium nitrite is then used to safely quench excess azide.
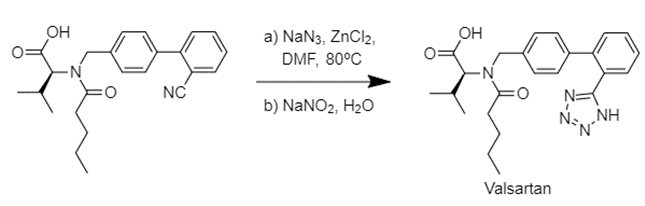
Nitrosamines can be formed by the reaction of a secondary amine with nitrite. Therefore, it is suspected that NDMA in Valsartan may come from the ZnCl2-catalysed disproportionation of DMF to dimethylamine and CO. Dimethylamine then goes on to react with sodium nitrite and the resulting product is NDMA.
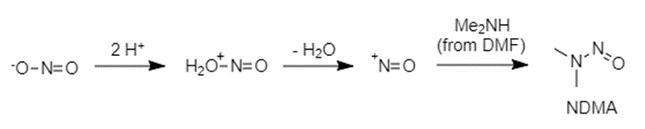
The ICH has published guidelines for the maximal concentration of NDMA in APIs and that number will be as low as 0.03 ppm after a 2 years transition period. Therefore, robust analytical methodologies to detect and quantify nitrosamines must be developed and implemented. However, such problems may also be circumvented by undertaking process research and development studies holistically.
Risk Mitigation
A well-designed route scouting and process design program will encompass questions such as safety, yield, impurity profile, environmental sustainability and economic viability. As such, instead of developing a purging step to lower the concentration of nitrosamines to an acceptable level, a robust, alternative route to the final product could be developed where conditions and reagents that may lead to the formation of these impurities are outright eliminated.
CatSci undertakes process research and development with an eye towards risk mitigation and can consistently optimise your chemical reactions and processes from lead optimisation through product launch and life-cycle management, enabling you to create affordable, best-in-class therapeutics.
Want to find out more?
Contact us at technical_enquiries@catsci.com or explore our website further to find out how CatSci can help you with developing control strategy.