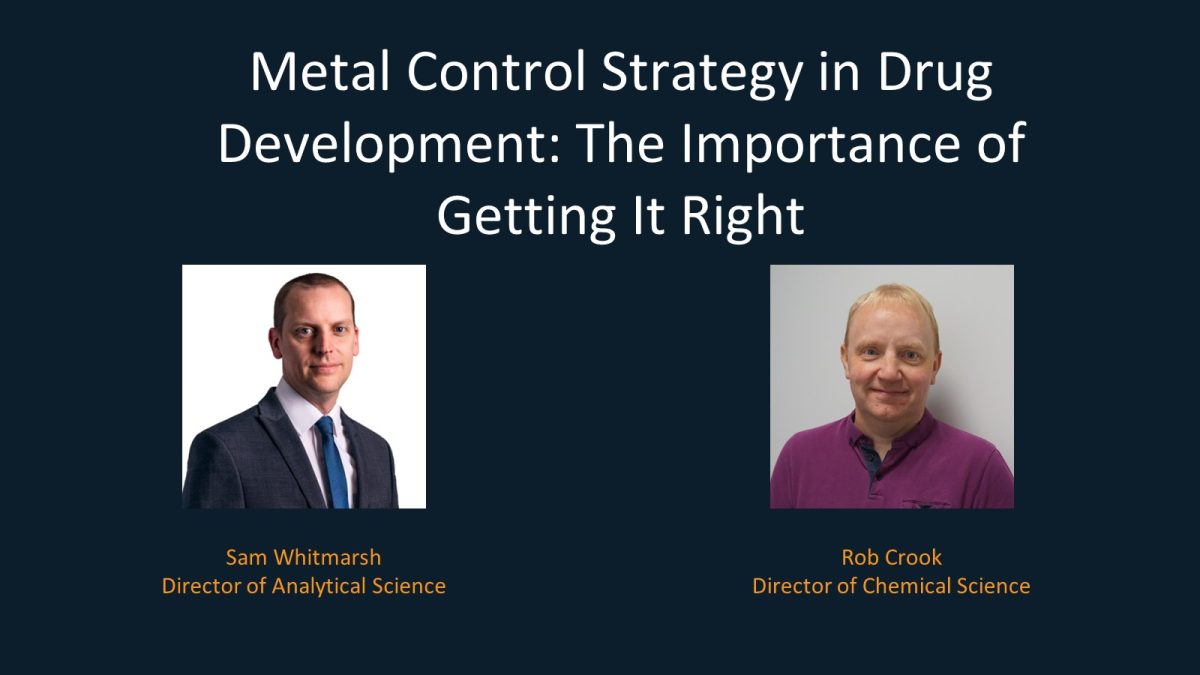
A Chemical Science blog, written by Sam Whitmarsh and Rob Crook
Introduction
Catalytic reactions are crucial in the development of pharmaceuticals. The increase in the use of biocatalysis and organocatalysis in recent years has been dramatic, but the field of catalysis is still dominated by metal catalysts, mainly of the precious metal variety. A lot of effort and research is ongoing to try and find alternatives to precious metal catalysts. One exciting area of catalysis, which is garnering large amounts of interest, is the use of earth abundant metals to carry out catalytic reactions (e.g. Cu, Ni, Fe, Mn, Co). Undoubtedly precious metal catalysed reactions will remain an important backbone of pharmaceutical synthesis; one of the most common reactions utilised to synthesise pharmaceuticals is the Suzuki reaction, with it being in the top 5 of the most used bond-forming reactions (Reference 1). One of the challenges of metal catalysed reactions is that the residual metals entrained at the end of the process need to be controlled to low levels due to their inherent toxicity. The level to which the metal will need to be controlled is dependent on several factors, including the specific chemistry of the metal, route of administration and dose being proposed. In most cases, metals will need controlling to low ppm levels. Specific guidance around control of metals can be found in ICH-Q3D elemental guidance (Reference 2).
In this blogpost, you will discover our robust metal control strategies and workflows that ensure alignment with the ICHQ3D requirements and ultimately patient safety.
Our Catalysis Workflow
At CatSci, we pride ourselves on our ability to develop high quality catalytic reactions, where we identify the best catalysts, understand and develop the process and ensure the quality of the product is well controlled. We have a strong track record of doing this across a wide range of substrates and chemical structures. To achieve this, we carry out a rigorous, well researched workflow practices.
- Assess current state of reaction and understand the needs of the customer.
- Ensure appropriate analytical capabilities are in place.
- Screen reactions in a medium to high throughput manner
- Understand quality of hits and develop processes for selected reaction/s, including detailed kinetics understanding.
- Design and develop a workflow to ensure that the product can be produced at the appropriate purity level.
- Analyse product to ensure appropriate quality is achieved, including appropriate control of residual metals.
The next section will focus on how to go about developing a process for the control of residual metals.
Our Metal Control Strategy
Once a reaction is complete, it is important to design a workflow to control the levels of residual metals to acceptable levels. As discussed, earlier control of metals in the final stage is crucial to ensuring patient safety but residual metals can interfere with subsequent chemistry (Reference 3) so a control strategy for residual metals is crucial to successful development of your product.
There are 4 main ways to control your metal level:
- Remove the metal via a crystallisation procedure with metal being left in the mother liquors
- Remove the metal via a liquid:liquid-extraction often using a chelating agent e.g. EDTA
- Filtration of solid metal particulates
- Utilisation of a solid phase adsorbent (carbon, silica, resin) to sequester the metal, followed by removal of the adsorbent by filtration
All these methods are valid and scalable ways of removing metals, some more desirable than others. Each can be used as a stand-alone technique or they can be combined. Most likely, one of the techniques would be used with a crystallisation procedure at the end to isolate the intermediate or API. For a more detailed review of metal control techniques, focussed on the removal of palladium, there is an excellent recent review in Organic Process Research and Development (Reference 3)
Fast and Robust Metal Analysis by ICP-MS
ICP-MS (inductively coupled plasma – mass spectrometry) is a quantitative, selective and highly sensitive method for the analysis of trace metals. For most catalytically relevant metals, limits of detection are well into the low part-per-trillion region, offering excellent scope for measurement of metals in even very high daily dose drug candidates. Methods can be established to monitor many analytes simultaneously in the same run with external calibration from multi component standards. For example, CatSci have a 64-element workflow designed for ultra trace analysis at ppt concentrations.
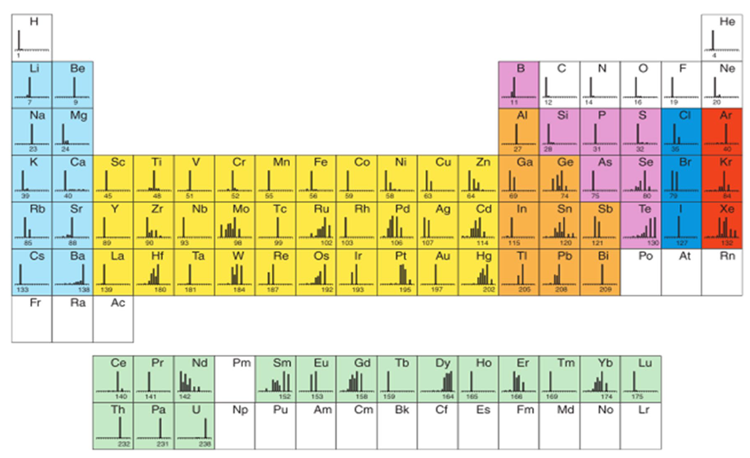
The CatSci ICP-MS instruments operate under GLP and GMP conditions and are based on USP <233> using a closed vessel microwave digestion sample preparation procedure. This is suitable for metals analysis in many organic matrices including small molecule API and formulated products containing excipients.
Our ICP-MS Instrumentation
CatSci uses Shimadzu’s ICPMS-2030 that provides superior sensitivity due to its newly developed collision cell and optimised internal structure.
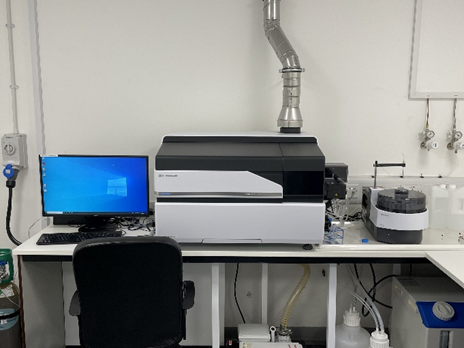
Thanks to the adoption of its proprietary mini-torch unit and provision of an Eco mode, the quantity of argon gas needed for analyses has been greatly reduced to the industry’s lowest levels. As a result, low running costs are assured. The Development Assistant function of the software automatically sets the optimal analysis conditions for quantitative analysis. Then, after measurements are complete, the Diagnosis Assistant function automatically checks the validity of the necessary data. While reducing the burden on the user, the efficiency of analyses is enhanced, and the reliability of the data can be increased. It complies with FDA 21 CFR Part 11.
The powerful sensitivity and throughput attributes of the instrumentation, combined with robust quality standards derived from our GLP approach, ensures we can produce detailed mapping of metal sequestration from synthetic processes and finally confirm metal concentrations in final API up to and including clinical batch release.
As well as supporting our own internal process development, we also offer rapid ICPMS metal analysis as a standalone service.
Summary
It is clear metal catalysed reactions play an important role in the synthesis of pharmaceutically active molecules and it will continue to be a key component of the organic chemist’s toolbox. Alongside the development of a high-quality reaction, it is also crucial that the purification of the intermediate, including the control of residual metals is considered. Partnering with an organisation who can support the reaction development, work-up, isolation as well as being able to undertake all appropriate analysis to support the work will give you the greatest chance of developing a process which delivers material and ultimately an API which is of the required quality to be used to treat patients.
References:
- J. Med. Chem 2016, 59, 4443-4458, Analysis of Past and Present Synthetic Methodologies on Medicinal Chemistry: Where Have All the New Reactions Gone? (acs.org)
- Q3D (R2) Step 5 Elemental impurities (europa.eu)
- OPRD 2023, 27, 9, 1585-1615 (acs.org)
- SN Applied Sciences 2019, 1, Guideline of inductively coupled plasma mass spectrometry “ICP–MS”: fundamentals, practices, determination of the limits, quality control, and method validation parameters (Springer)
Want To Find Out More?
Contact us at enquiries@catsci.com or explore our capabilities.
Authors: Sam Whitmarsh, Director of Analytical Science; Rob Crook, Director of Chemical Science