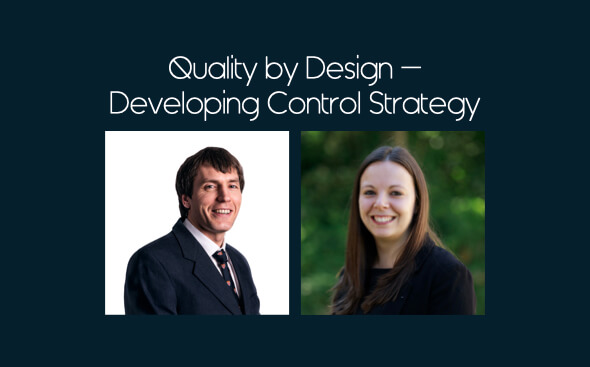
ICH Q8(R2) defines ‘control strategy’ as “A planned set of controls, derived from current product and process understanding that ensures process performance and product quality.” The concept is not new, however, controlling API quality with intermediate and end product testing can simply be thought of as a minimal control strategy. Reduced end-product testing enabled by upstream testing and comprehensive process understanding, in line with the Quality by Design (QbD) paradigm, is synonymous with an enhanced control strategy.
Key Parameters to Consider
It is important, when focusing on the patient centric requirements of QbD, not to relegate the consideration of the process performance aspect. The customers of a control strategy are not just Health Authority reviewers, but the manufacturing groups that need to implement the manufacturing process in their facility before and long after a product has been approved for patient use. This quality and manufacturability bifurcation has spawned the term ‘manufacturing control strategy’, in recognition of the fact that as well as ensuring the delivery of a quality product, its components need to deliver on cost, cycle time, efficiency, energy consumption, environmental footprint, operator safety and other aspects of ‘manufacturability’.
A manufacturing control strategy is much more than the commitments that make it into a clinical or marketing application. It has more than one layer and includes the controls that allow these commitments to be met, monitoring programmes and the procedures that govern how manufacturing chemists and QC scientists operate. When assessing a change to a control strategy component, the impact on both the patient and the business should be considered, as shown in the Figure below.
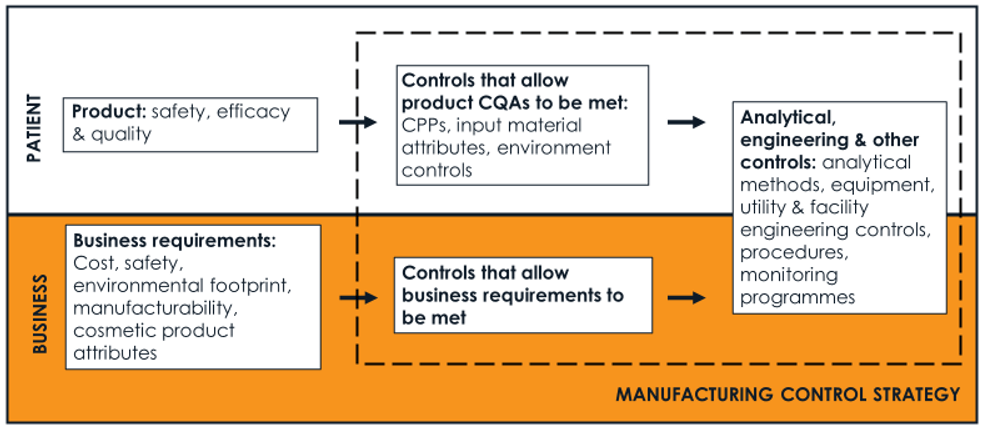
Putting It Into Practice
Being able to visualise the manufacturing control strategy, and the understanding that sits behind its construction, has multiple benefits. Visualisation highlights weaknesses that could impact product quality or process performance ahead of making a planned change in scale, equipment, facility or the quality of an input material – alongside empowering continuous improvement and allowing new product knowledge and process understanding to come to light. Where visualisation is inadequate, it brings uncertainty as to whether the knowledge exists or simply cannot be found, leaving manufacturing groups partially sighted when asked to accommodate changes in the supply chain, investigate deviations or changes in risk assessment imposed by external regulatory authorities.
Key information may also become lost during handovers between groups. In this regard, a customer’s approach to and expectations around manufacturing control strategy development, transfer, updating and maintenance should be one of the first things discussed with a CRO or CDMO partner at the outset of a contract.
How early should you start thinking about the development of a manufacturing control strategy? It makes sense to begin discussions with your selected vendor regarding the ideal set of controls associated with a post approval manufacture as soon as the synthetic sequence envisaged for the commercial manufacture of an API has been decided. As an example, this could include aspiring to controlling a particular attribute through process control, rather than testing to an envisaged specification acceptance criterion. Data are then gathered to establish if this position can be supported. Building and visualising a manufacturing control strategy that delivers for the patient and the business is clearly a complex and continuous activity, but a crucial one if new products are to make it onto the market and established products are to stay there.
Want to find out more?
Contact us at technical_enquiries@catsci.com or explore our website further to find out how CatSci can help you with developing control strategy.